Polyester low elastic yarn can be classified based on various characteristics such as its composition, denier (thickness), elasticity, and application. Here are some common classifications:
Composition:
a. 100% Polyester Low Elastic Yarn: Yarn made entirely of polyester fibers.
b. Polyester Blended Low Elastic Yarn: Yarn that combines polyester fibers with other materials such as cotton, rayon, or nylon.
Denier:
a. Fine Denier Polyester Low Elastic Yarn: Yarn with a lower denier, typically ranging from 20D to 150D.
b. Medium Denier Polyester Low Elastic Yarn: Yarn with a medium denier, usually ranging from 150D to 600D.
c. Thick Denier Polyester Low Elastic Yarn: Yarn with a higher denier, typically above 600D.
Elasticity:
a. High Elastic Polyester Low Elastic Yarn: Yarn with a higher level of elasticity, providing greater stretch and recovery.
b. Medium Elastic Polyester Low Elastic Yarn: Yarn with moderate elasticity, offering a balance between stretch and recovery.
c. Low Elastic Polyester Low Elastic Yarn: Yarn with minimal elasticity, providing limited stretch and recovery.
Application:
a. Apparel Polyester Low Elastic Yarn: Yarn used in the production of clothing, such as sportswear, swimwear, lingerie, and stretchable fabrics.
b. Home Textile Polyester Low Elastic Yarn: Yarn used for home furnishing purposes, including bed linens, upholstery, curtains, and rugs.
c. Industrial Polyester Low Elastic Yarn: Yarn used in industrial applications, such as sewing threads, webbings, belts, ropes, and automotive textiles.
d. Medical Polyester Low Elastic Yarn: Yarn used in medical and healthcare products, including elastic bandages, compression stockings, and orthopedic devices.
Besides,The production of polyester low elastic yarn involves several steps in the manufacturing process. Here is an overview of the typical production steps:
Polymer Production: The process begins with the production of polyester polymer, which involves reacting purified terephthalic acid (PTA) or dimethyl terephthalate (DMT) with ethylene glycol (EG). This reaction forms a polyester melt, which is then extruded into thin strands known as polyester chips or pellets.
Melt Spinning: The polyester chips are melted and extruded through spinnerets, which are specialized metal plates with small holes. The extruded molten polymer forms continuous filaments. For low elastic yarn, an additional step is introduced during melt spinning to incorporate elastic components into the polyester. This can be achieved by co-extruding a core filament made of an elastic material, such as spandex or elastane, with the polyester filament.
Cooling and Solidification: The newly formed filaments pass through a cooling chamber where they are rapidly cooled by air or water, solidifying the filaments and giving them strength.
Drawing: The solidified filaments undergo a drawing process to increase their orientation and molecular alignment, which enhances their tensile strength and elasticity. Drawing is typically done by passing the filaments through heated rollers at controlled speeds, applying tension to align the polymer chains.
Heat Setting: In order to stabilize the newly oriented molecular structure and impart permanent elasticity to the filaments, they undergo a heat setting process. The filaments are exposed to high temperatures while being stretched slightly, allowing the molecular chains to relax and set in the stretched position.
Twisting: The heat-set filaments are then twisted together to form yarn. Twisting improves the yarn's strength, stability, and uniformity. The twisting process involves passing the filaments through a series of rotating spindles or bobbins, which twist them together in a controlled manner.
Winding and Packaging: The twisted yarn is wound onto bobbins or cones, ready for further processing or direct distribution. The yarn is packaged in suitable containers, such as cardboard cones or plastic spools, to protect it during transportation and storage.
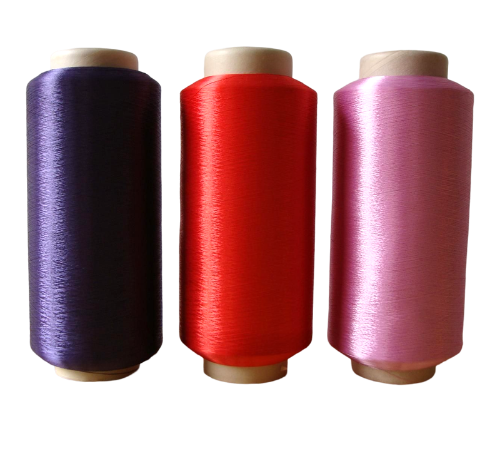
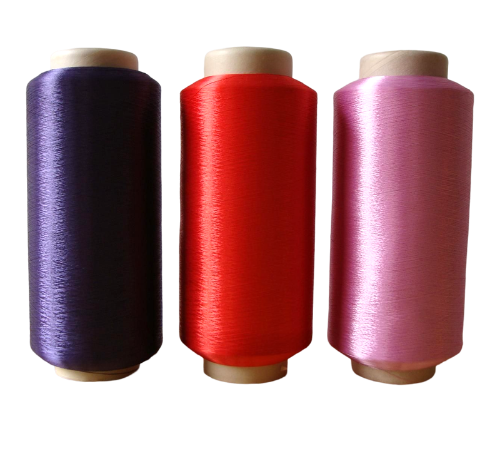